Explore Surface Techniques in EBI’s Perfume Atomizers
In the world of perfume packaging, presentation is as essential as the scent itself. Perfume atomizers, designed for convenience and elegance, require meticulous attention to their surface finish to attract consumers and enhance user experience.The artistry and technology behind these sprayers involve a range of surface processes, each contributing to the overall aesthetics, durability, and functionality of the product. From sophisticated techniques like water transfer printing and laser engraving to modern approaches such as diamond CNC cutting and rubber printing, these processes transform simple containers into stylish accessories.
EBI delves into the various surface processes used in the production of perfume atomizers,exploring their advantages and disadvantages to provide customers with a better, more comprehensive and more diverse packaging service for their brands.
1.Water transfer printing
Water transfer printing, commonly known as water decals, refers to the transfer of patterns and patterns on the water-soluble film to the substrate through the pressure of water.
Advantages:
- Complex Designs: Water transfer printing can produce intricate and detailed designs, covering curves and contours effectively.
- Versatility: It can be applied to various materials, including plastic, glass, and metal, making it suitable for different types of perfume sprayers.
- Seamless Coverage: The process allows for seamless application over complex shapes, eliminating issues like alignment and edge visibility.
- Vivid Colors and Patterns:This technique can replicate detailed images with vibrant colors, enhancing the aesthetic appeal of the sprayer.
- Customization: Brands can easily create unique and personalized designs, helping to differentiate their products in a competitive market.
Disadvantages:
- Setup Complexity: The setup process can be complex and may require specialized equipment, which can increase initial costs.
- Environmental Factors: The process involves the use of chemicals and inks that may raise environmental concerns, although there are eco-friendly options available.
- Durability Concerns: Depending on the quality of the materials and application, water transfer prints may be less durable than screen printing, especially in high-contact areas.
- Limited Production Speed: The process can be slower than other printing methods, particularly for larger runs.
- Potential for Imperfections: If not done carefully, issues like bubbling or misalignment can occur, affecting the final appearance of the product.
2.Heat transfer printing:
Heat transfer printing is another widely used perfume packaging material surface processing technology, which transfers pre-printed patterns or text to the packaging surface. The heat transfer printing process is simple and can achieve fine visual effects on packaging materials of different shapes. It is worth mentioning that heat transfer printing can create a variety of visual effects such as metallic feel and luster, further enhancing the high-end image of the product.
In summary, heat transfer printing offers vibrant, durable designs suitable for various materials, but it comes with some limitations in color range and production efficiency.
Advantages:
- High-Quality Graphics: Heat transfer printing allows for vibrant colors and intricate designs, enhancing the visual appeal of the atomizers.
- Durability: The prints are generally resistant to fading and scratching, ensuring that the designs remain intact over time.
- Versatility: This method can be applied to various materials, including glass and plastic, making it suitable for a wide range of atomizer designs.
- Eco-Friendly Options: Many heat transfer printing processes use water-based inks, reducing the environmental impact compared to traditional printing methods.
- Cost-Effective for Small Runs: It can be a cost-effective solution for smaller production runs or custom designs, as setup costs are relatively low.
Disadvantages:
- Limited Color Range: While capable of vibrant prints, there may be limitations on certain color effects or gradients compared to other printing techniques.
- Temperature Sensitivity: The process involves heat, which can affect heat-sensitive materials, potentially limiting design choices.
- Complex Process: The setup for heat transfer printing can be complex and may require specialized equipment and training.
- Adhesion Issues: Depending on the material of the atomizer, there may be challenges with the print adhering properly, leading to peeling or fading over time.
- Production Speed: Heat transfer printing can be slower compared to other mass production methods, which may affect turnaround times for large orders.
- Inconsistency: The pattern of the perfume atomizers cannot be guaranteed at the time of production.
3.Anodic oxidation process:
Oxidation refers to the chemical reaction between an object and the oxygen in the air, called oxidation reaction, which is a natural phenomenon. The oxidation described here refers to the surface treatment process of hardware products.
Process flow: alkaline washing – washing – bleaching – washing – activation – washing – aluminum oxidation – washing – dyeing – washing – sealing – washing – drying – quality inspection – storage.
The role of oxidation: protective, decorative, coloring, insulating, improving the bonding force with organic coatings, and improving the bonding force with inorganic coating layers.
Secondary oxidation: By blocking or deoxidizing the surface of the product, the product is oxidized twice, which is called secondary oxidation.
1) Different colors appear on the same product. The two colors can be close or different.
2) The production of the protruding LOGO on the surface of the product. The protruding LOGO on the surface of the product can be stamped and formed, or obtained by secondary oxidation.
Secondary oxidation is a process that can give metals or surfaces a distinctive, aged appearance. For a product logo on perfume atomizers, using secondary oxidation could create an elegant and vintage aesthetic that conveys a premium or artisanal quality. However, it also has its limitations.
Advantages:
- Premium Aesthetic: Secondary oxidation can add a sophisticated, antique or vintage look, making the logo appear more luxurious and high-end.
- Durability: The oxidation layer can serve as a protective coating, potentially making the logo more resistant to minor abrasions and wear.
- Unique Visual Appeal: Each oxidized surface may develop a slightly different pattern, giving each atomizer a unique look that could appeal to customers seeking uniqueness.
- Compatibility with Metal: Oxidation works well on metals (like brass or copper), which are often used for luxury perfume packaging, enhancing the overall aesthetic.
Disadvantages:
- Limited Color Options: Secondary oxidation often results in darkened or muted colors (blues, greens, grays), which may limit the vibrancy and color choices for logos.
- Potential for Inconsistency: Because oxidation depends on environmental factors, the finish can vary between batches, possibly leading to inconsistency in branding.
- Surface Sensitivity: Over time, oxidation can wear off or change further, especially if the product is exposed to moisture or handling, potentially altering the logo’s appearance.
- Higher Production Cost: Oxidizing metal surfaces can be more costly than simpler logo application methods, affecting production budgets.
4.Spray Coating Process:
Spray coating is a versatile technique used for applying logos or designs to various surfaces, including metal or glass perfume atomizers. Spraying generally includes oil spraying, powder spraying, etc., and the common one is oil spraying. The sprayed coating is commonly known as paint, and the coating is composed of resins, pigments, solvents, and other additives. Plastic spraying generally has two layers of paint, the color on the surface is called topcoat, and the most transparent layer on the surface is called protective paint.
Introduction of spraying process:
1) Pre-cleaning. Such as electrostatic dust removal.
2) Spray the top coat. The topcoat is generally the color seen on the surface.
3) Dry the finish. It is divided into room temperature natural drying and special oven drying.
4) Cool the finish. Dedicated oven drying requires cooling.
5) Spray protective paint. Protective paint is generally used to protect the topcoat, most of which are clear paints.
6) Curing the protective paint.
7) QC inspection. Check if the requirements are met.
Rubber oil, also known as elastic paint, feel paint, rubber oil is a two-component high elastic hand paint, the product sprayed with this paint has a special soft touch and high elastic surface feel. The disadvantage of rubber oil is high cost, general durability, and easy to fall off after a long time. Rubber oil is widely used in communication products, audio-visual products, MP3, mobile phone casings, decorations, leisure and entertainment products, game consoles, beauty equipment, etc.
UV paint is the English abbreviation of Ultra-VioletRay. The commonly used UV wavelength range is 200-450nm. UV paint can only be cured when exposed to ultraviolet light.
2) The characteristics of UV paint: transparent and bright, high hardness, fast fixing speed, high production efficiency, protective topcoat, hardening and brightening the surface.
Spray coating is one of the most common post-processing techniques in modern perfume bottle production. Through this process, the chosen colors can be applied to the bottles in various ways such as partial spray, gradient spray, two-tone spray, and rainbow spray. This significantly enriches the color presentation of the perfume bottles, allowing for a wide range of creative expressions.In summary, spray coating is a flexible, cost-effective way to add a logo with a professional, polished look, especially if color and finish consistency are priorities. However, it may not be as durable as some other methods and requires careful handling to avoid imperfections.
Advantages:
- Customizable Colors and Finishes: Spray coating offers a wide range of colors and finishes (matte, gloss, metallic, etc.), allowing for vibrant, eye-catching logos that can align closely with brand aesthetics.
- Consistent Quality: This process can produce uniform, consistent results across large batches, ensuring that logos look identical across all units, which is essential for brand consistency.
- Durability: High-quality spray coatings can be resistant to scratches, fading, and environmental factors like UV exposure and moisture, preserving the logo’s appearance over time.
- Precision: When combined with stencils or masking techniques, spray coating allows for precise logo application on curved surfaces, which is particularly useful for cylindrical or uniquely shaped perfume atomizers.
- Cost-Effective for Large Batches: Spray coating can be a relatively affordable option for large-scale production, as it can be applied quickly and efficiently across many units.
Disadvantages:
- Potential for Wear and Tear: Although durable, spray coatings can still chip or wear off over time, especially if the atomizer is frequently handled or exposed to harsh conditions.
- Surface Preparation Requirements: To ensure adhesion, surfaces often need thorough cleaning or priming before spray coating, which can add to production time and costs.
- Environmental Concerns: Some spray coating materials may release volatile organic compounds (VOCs) that can be harmful to the environment and require proper ventilation and disposal practices.
- Limited Texturing Options: While spray coating offers various color and gloss options, it may not achieve textured finishes like engraving or embossing can, which could limit design flexibility.
- Possibility of Overspray and Inconsistency: If not done carefully, spray coating can result in overspray (unwanted paint around the logo) or variations in thickness, which might affect the final look.
5. UV Electroplating Process:
The UV plating process, also known as UV electroplating, combines traditional electroplating techniques with a UV-curable layer to produce a durable, high-gloss finish. This process is typically used for products that require a premium metallic look and added durability. Here’s a breakdown of the UV plating process flow:
Surface Preparation – Clean and, if necessary, etch the substrate.
Base Coating – Apply and cure a primer for better adhesion.
Electroplating – Add a conductive layer and electroplate with the desired metal.
UV Coating Application – Apply a UV-curable protective topcoat.
UV Curing – Cure the UV coating with UV light.
Quality Inspection – Check for defects and test durability.
Final Cleaning and Packaging – Prepare the components for shipment.
Advantages:
- High Durability and Scratch Resistance: The UV electroplating process creates a hard, resilient coating that is highly resistant to scratches, fading, and everyday wear, helping the logo remain vibrant over time.
- Premium Metallic Finish: UV electroplating produces a bright, glossy, and reflective metallic effect, giving the logo a luxurious, high-end appearance that is often sought after in the perfume industry.
- Enhanced Color Stability: Unlike traditional electroplating, UV electroplating includes a UV-curable layer that stabilizes the color, preventing it from fading or discoloring due to light exposure or the ingredients in the perfume.
- Environmental Friendliness: Compared to some traditional electroplating methods, UV electroplating often requires fewer harmful chemicals and produces less waste, making it a more eco-friendly option.
- Consistency Across Batches: The precision of the UV electroplating process ensures a consistent and high-quality finish across large production batches, which is crucial for branding consistency.
Disadvantages:
- Higher Production Costs: UV electroplating is generally more expensive than other logo application methods due to the advanced technology and materials involved, which could impact production budgets.
- Complex Process Requirements: This process requires specialized equipment and expertise, which can increase setup time and require additional training or outsourcing to experienced suppliers.
- Limited Color Options: While UV electroplating provides a stunning metallic effect, it’s typically limited to metallic shades like gold, silver, and chrome. Custom colors can be more challenging and costly to achieve.
- Potential for Peeling if Improperly Applied: If the surface isn’t perfectly clean or prepared, or if there are application issues, the UV coating can peel, especially with prolonged exposure to heat or humidity.
- Longer Production Time: UV electroplating generally takes longer than simpler processes like spray coating, as it involves multiple layers and curing steps, which can slow down production and increase lead times.
6. Glitter painting:
Glitter painting is a decorative process that involves applying a glittery finish to surfaces, providing a sparkling and eye-catching appearance. This process is commonly used on products like perfume atomizers to create a unique, glamorous look. Here’s an overview of the typical process flow for glitter painting:
- Surface Preparation – Clean and, if necessary, sand or prime the surface.
- Base Coat Application – Apply a solid base color and allow it to dry.
- Glitter Paint Application – Apply glitter paint in thin, even layers.
- Top Coat Application – Seal with a clear protective coat for durability.
- Curing – Allow the coating to fully cure.
- Quality Control and Inspection – Check for even coverage and quality.
- Final Cleaning and Packaging – Prepare for shipment.
Advantages:
Visually Striking: Glitter paint adds sparkle and shine, making the logo stand out and catch the eye, which can be very appealing for a high-end or glamorous brand identity.
Customizable Aesthetic: Glitter paint can be adjusted for color, size, and intensity, allowing brands to choose the precise level of shimmer that best matches their aesthetic.
Perceived Value Enhancement: The glitter effect can give the product an upscale, luxurious appearance, potentially adding to its perceived value and enhancing its appeal to customers.
Flexible with Brand Colors: Glitter paint is available in a wide range of colors, so it can be tailored to match brand colors, unlike some other finishes that might limit color options.
Disadvantages:
Durability Concerns: Glitter paint may be prone to flaking or fading over time, particularly if it’s not sealed with a protective coating. This can be a drawback for a product that customers expect to last.
Costly Production: Applying glitter paint typically involves a more complex production process, especially when ensuring that the glitter particles are uniformly distributed. This can increase production costs, particularly for intricate logos.
Potentially Overpowering for Some Brands: While glitter works well for glamorous or bold brands, it may not suit minimalist or classic brands and could potentially detract from a logo’s legibility or simplicity.
Complex Maintenance: Glitter paint requires careful maintenance to preserve its sparkle, as dust or oils can dull the finish over time. This can be a challenge for an everyday product like a perfume atomizer.
Increased Environmental Concerns: Some glitter materials are not eco-friendly (e.g., microplastics), which may be a concern for brands focused on sustainability or environmentally conscious production.
7. Brushed finishing:
A brushed finishing process for a perfume atomizer’s product logo can add a unique and appealing texture that influences the look and feel of the product. This finish involves creating a fine-lined texture by sanding or brushing the metal surface, typically with specialized tools. Using a brushed finish for perfume atomizer logos can create a sophisticated and durable look but may require careful consideration of brand aesthetics, logo complexity, and production costs.Here’s an overview of the typical process flow for brushed finishing:
- Surface Preparation – Clean and deburr the surface.
- Sanding (Optional) – Smooth out imperfections.
- Brushing – Apply a uniform, directional brushing pattern.
- Inspection and Touch-Up – Check texture consistency and correct if needed.
- Cleaning and Protective Coating (Optional) – Clean and protect the surface.
- Quality Control and Final Inspection – Confirm quality and uniformity.
Advantages:
Enhanced Aesthetic Appeal: Brushed finishes have a refined, matte look that can add a touch of elegance and sophistication, making the product appear more premium.
Fingerprints and Smudges: The matte texture of brushed finishes makes fingerprints and smudges less visible, keeping the atomizer looking cleaner over time.
Durability and Scratch Resistance: The brushed texture can help hide minor scratches and abrasions, maintaining a better appearance even after extended use.
Improved Grip: A brushed finish can provide slight friction, which makes the atomizer less slippery to handle, potentially enhancing usability.
Disadvantages:
Increased Production Cost: The brushing process requires additional labor and machinery, which may raise production costs, especially for high-precision logos.
Potential for Uneven Finish: If not done correctly, brushing can result in an uneven texture or visible brush strokes, which may detract from the logo’s clarity and overall appearance.
Limited Color and Finish Options: Brushed finishes are often restricted to matte or satin finishes, which might limit design options, particularly for brands looking for vibrant or highly polished looks.
Difficulties in Achieving Fine Details: Brushed finishes may blur very fine details in a logo, especially for intricate or small designs, making this technique less suitable for logos with detailed or delicate elements.
Logo customization process
1.Screen printing :
Screen printing is an ancient but widely used printing method.Overall, screen painting can be a great choice for branding perfume atomizers, especially for larger runs and designs that benefit from durability and vibrancy, but it may not be ideal for all situations, particularly small batches or highly detailed multi-color designs.
Advantages:
- Durability: Screen printing creates a robust bond with the surface, making the designs resistant to wear and fading over time.
- Cost-Effective for Bulk Production: When producing large quantities, screen printing can be more economical than other methods, like digital printing.
- Vibrant Colors: This technique allows for bright and vivid colors, enhancing the overall appearance of the perfume atomizers.
- Customization: It enables detailed and intricate designs, allowing brands to express their identity effectively.
- Texture and Finish Options: Screen printing can produce various finishes (matte, glossy) and even textured effects, adding to the visual appeal.
Disadvantages:
- Setup Costs: The initial setup for screen printing can be expensive, particularly for small production runs.
- Limited Color Range: Each color requires a separate screen, which can be limiting and increase costs if many colors are needed.
- Time-Consuming: The process can be slower than other printing methods, particularly for complex designs.
- Environmental Considerations:Some inks and solvents used in screen printing can be harmful to the environment, although eco-friendly options are becoming more available.
- Less Flexibility for Changes: Once a screen is created, altering the design requires starting the process anew, which can be inefficient.
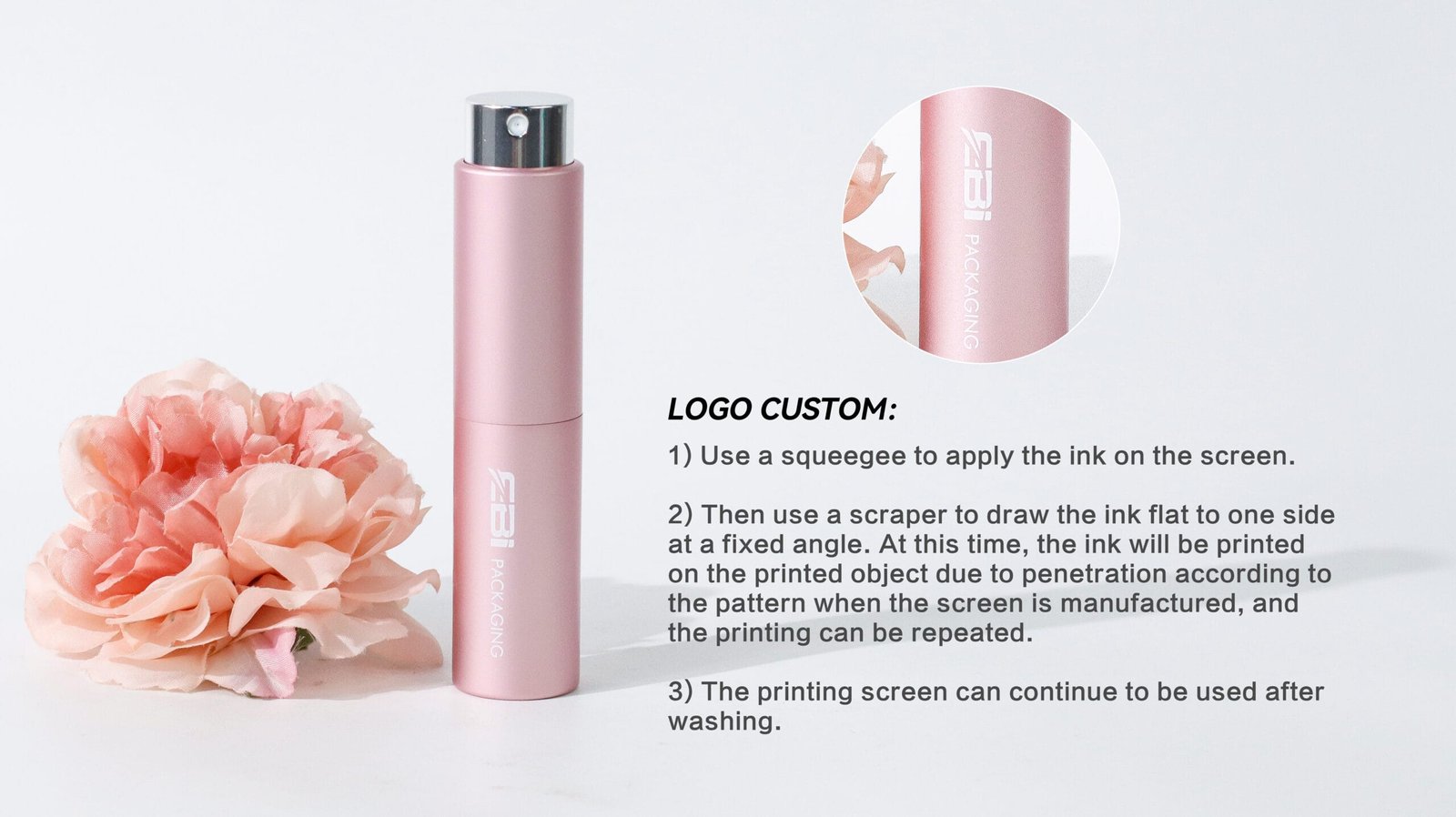
2.Laser engraving:
Laser engraving, also called laser engraving or laser marking, is a process of surface treatment using optical principles.Overall, while laser engraving offers significant benefits in terms of customization and durability, it also presents challenges that need to be considered, especially regarding material compatibility and costs.
Advantages:
- Precision and Detail: Laser engraving allows for intricate designs and high precision, enabling complex patterns and fine text that can enhance the aesthetic appeal of the atomizers.
- Durability: The engraving is permanent and resistant to wear, ensuring that the design remains intact over time, even with frequent handling.
- Customization: It enables personalized designs, such as names or special messages, making the atomizers unique and perfect for gifts or branding purposes.
- Speed and Efficiency: Laser engraving is a fast process compared to traditional engraving methods, allowing for quick production and turnaround times.
- Eco-Friendly: Since laser engraving doesn’t involve inks or harmful chemicals, it can be considered a more environmentally friendly option.
Disadvantages:
- Cost: Initial setup costs for laser engraving equipment can be high, and this may not be economical for small-scale production.
- Material Limitations: Not all materials used in perfume atomizers are suitable for laser engraving. Some plastics may not engrave well, affecting the design quality.
- Heat Sensitivity: The process generates heat, which can potentially damage sensitive components of the atomizer if not carefully managed.
- Surface Preparation: The surface of the atomizer may need to be prepared or treated to ensure the engraving adheres well, which can add extra steps to the production process.
- Limited Color Options: Unlike printing, laser engraving typically only results in a single color or shade (often a darker or lighter version of the material), which can limit design creativity.
3.Embossing
The embossing process is a popular choice for adding a three-dimensional effect to product logos on perfume atomizers. By raising or depressing parts of the logo design on the surface, embossing creates a tactile, visually distinct logo that can add a sense of luxury. Here are some key advantages and disadvantages of using embossing for perfume atomizer logos.
Advantages:
Enhanced Tactile Appeal: Embossed logos provide a textured surface, which can make the atomizer more engaging and memorable to the touch, enhancing the customer’s sensory experience.
Elegant and Premium Look: Embossed logos often have a high-end appearance associated with luxury, sophistication, and attention to detail, which suits the image of premium perfume products.
Durability: Unlike printed or painted logos, embossing does not fade or wear off easily since it is a part of the material structure, making it a durable option for products frequently handled.
No Additional Chemicals or Inks: Embossing is a clean process that does not require extra paints, inks, or coatings, which can reduce the need for added chemicals and align with eco-friendly production practices.
Brand Differentiation: Embossed logos are less common in mass-market products, making them a unique choice that helps a brand stand out from competitors by emphasizing quality and craftsmanship.
Disadvantages:
Higher Production Costs: Embossing requires specialized tooling (dies or molds) and equipment, which can increase production costs, especially if custom designs are needed for different product lines.
Limited Design Complexity: Highly intricate or detailed designs may not translate well in embossing, as fine lines or complex shapes can become distorted or lose clarity in the raised format.
Surface Constraints: Embossing is generally more suitable for flatter surfaces. Curved or irregular shapes, like the cylindrical body of a perfume atomizer, can complicate the embossing process and limit its applicability.
Increased Production Time: Setting up embossing equipment and aligning designs precisely can take longer than simpler printing or painting processes, potentially slowing down production.
Limited Color Options: Embossing itself does not add color, so the logo will typically match the base material color. For brands that require vibrant or contrasting logo colors, additional processes like painting or inking may be necessary, adding further steps.
Tooling Wear and Maintenance: Embossing tools (dies) can wear out over time, especially in high-volume production. This wear can lead to inconsistencies in the logo’s appearance and require periodic replacement or maintenance.
SOBRE NOSOTROS
EBI es un proveedor de soluciones de envasado sostenible fundado en 2009. Ipurso, una marca de EBI, se especializa en necesidades de envasado y diseño de pequeña capacidad para la industria del perfume y la aromaterapia.
servicios. Nos centramos en el suministro de atomizadores para perfumes, frascos roll-on, frascos cuentagotas, tubos para inhaladores, etc.
- sale1@ebi-china.com
- +86-15170062480
- De lunes a viernes, de 9.00 a 18.00 horas